Avoiding the Most Common Construction Defects
BUSTAMANTE ENGINEERING STAFF • January 27, 2020
What to Look for and How to Prevent Problems
Construction defects are common, though most are usually fairly inconsequential. However, the most dangerous issues could risk damage to people or the property itself. Regardless of whether a defect is major or minor in nature, a problem remains: defects typically aren’t discovered until long after completion of the work.
Which are the Most Common?
Generally, construction defects refer to a deficiency in the construction process – be that in design, materials, or workmanship – which leads to a failure in some aspect of the structure. They can range from visible, often minor issues to real problems that can remain hidden for years before leading to catastrophic failure. What follows are the most-cited problems.
- Aesthetic Issues
- Not surprisingly, most everyone mentioned drywall cracks and nail pops. The best way to avoid them is by paying for good work. A bargain drywaller might take shortcuts like skipping coats and not leaving sufficient drying time between coats. These problems are commonly attributed to “settling” but drying the framing helps with a range of cosmetic issues - not only drywall pops, but also cracks in drywall, squeaks in floors and stairs, interior trim joints that open up, and caulking that pulls and cracks. Fast construction schedules accelerate these problems, because the house framing barely has any time to dry on its own before the next stage of construction begins. Such short cycle houses are notorious for having a large number of drywall cracks and other cosmetic defects after a year of heating and cooling by the occupants.
- Annoying Squeaks
- Squeaky subfloors can be a big source of complaints. Upgrading to engineered subflooring will help eliminate the problem. These panels feature a built-in underlayment that allows the convenience of using only one layer under certain finish flooring. The type of finish flooring can help guide the choice of the correct subfloor. Rated sheathing may be used with an underlayment for vinyl, ceramic tile or fully adhered carpet. An underlayment is optional when used with hardwood. When using carpet and pad, it allows for completely bypassing installation of underlayment. Also, it’s crucial to use a high-quality polyurethane subfloor adhesive because old school glues don’t stick to the newer subfloor panel products.
- Sagging Floors
- Framing errors can lead to uneven floors. The problem has to do with the way today’s homes are designed. With today’s open floor plans, some designers forget to account for the loads the floor will bear. For instance, a large kitchen with an 8x12 granite topped island was constructed with no bearing wall under the joists. The kitchen floor ended up settling and sloping toward the island. The builder had to go back, jack the floor up, and triple the joists. Settling can also occur in rooms with thickset tile or stone floors.
- Roof & Sidewall Ripples
- Another common problem is sheathing that swells and buckles, telegraphing waves through the cladding or roofing. The fix is simple: Leave a 1/8-inch gap between panels. But some framers seem unaware of this advice. Be sure to inspects the sheathing before it’s covered and add gaps where needed. Swelling can also be a problem with fiber-cement siding, where joints between horizontal runs may need to be gapped and filled with sealant. Products that require caulking at joints do so for good reason. If this advice is ignored, the board will soak up water and swell at the edges.
- Damp Basements
- A leaky foundation is the one of the most challenging defects to take care of because the repair costs can be high. The basement is more likely to stay dry with a sound structure. Even a hairline crack can let moisture into the wall. Many homes can have water seepage at the slab-to-wall connection. Wide footings with plenty of steel reinforcing over thoroughly compacted soil is recommended. Even without visible water, a damp basement or crawlspace can turn into a mold generator. The most important ingredient is a gap between the foundation wall and the surrounding soil to relieve hydrostatic pressure. Without a gap, hydrostatic pressure can force an enormous amount of water through even the smallest penetrations in the wall. Typically, a dimple mat covered by a geotechnical fabric to create this gap is used to allow free drainage to the footing perimeter drains.
- Stucco Failures
- Getting stucco right seems to be a real challenge and is the most common problem reported. Mistakes that are common with stucco frequently occur with adhered masonry products, as well. Errors fall into three categories:
Missing Joints - When the stucco expands or contracts, it cracks, letting water into the structure. The standards that govern stucco specify control joints every 144 square feet. But they often get left out because of ambiguity in implementation of these standards, and because some builders don’t like the look of control joints. Or using a flexible sealant where the stucco meets another material is often overlooked.
Wrong Mix - Too much sand can make the mix weak and prone to cracking. Too little sand leaves it brittle, so cracking tends to be dramatic. When brittle stucco cracks it can even shear the metal lath beneath the stucco. The solution to both problems is to use premixed stucco.
Poor Hydration - Stucco needs to be kept hydrated for a few days after it’s applied. Some installers skip this step which causes the pH to remain too high to effectively hold paint. - Leaky Transitions
- With exterior flashings, the most problematic spots are where brick or stone veneer meets another type of siding. Where a roof meets a wall, the roofer will often neglect to install kick-out flashing that directs water into the gutter. When it’s missing, water can run down the wall below the gutter, working its way behind the siding and rotting the sheathing. The advice is to provide a scope of work that details exactly how the flashings are to be done and to make sure a job supervisor is on site to check the work.
- Penetration Detailing
- Installers have gotten better in recent years when it comes to window flashing. The one exception is the sill pan. Aluminum windows especially need a pan because installers can accidentally break the seal at the bottom corners. By the time the homeowner sees a stain on the wall, there is already rot in the structure. Leaky pipe and vent penetrations are also common. When a hole for a gas line or dryer vent is cut, it needs to be flashed to the WRB. This problem won’t be fixed until installers start taking wall penetrations as seriously as roof penetrations.
- Flat-Roof Leaks
- Modern architecture is always popular and modern architecture means flat roofs. While today’s roofing membranes are durable, it can be a challenge to integrate the roof and wall flashings in these situations. Even the smallest defect can cause a leak. Implementing strategies like using membranes on walls and parapets and bringing the roofer in early to integrate the membrane with the roof flashing can help eliminate problems.
- Hot & Cold Spots
- Comfort complaints are rampant, and the fault often lies with the ductwork. A lot of residential ducts have excessively high static pressures causing the mechanical equipment to run longer and to start/stop more often, making it more prone to breakdown and premature failure. The causes behind excessive pressures range from undersized ducts, to excessive bends, to sagging flex duct. Many homes also have inadequate return paths, leaving some rooms too hot and others too cold. Another comfort killer is ducts that are run in unconditioned spaces without being properly insulated or sealed, wasting more than a ton of heating or cooling capacity. The best way to avoid these problems is consult closely with the mechanical contractor during the design phase.
- Custom Showers - Complex showers need a higher level of waterproofing. Upgraded master baths with custom showers that feature built-in seats and multiple showerheads are a hot option among homeowners. They tend to be on the second floor above a living space, so leak-proofing is crucial. Installations can develop pinhole leaks that are hard to detect but that let mold and rot slowly build up in framing cavities. If the seat is built into a corner, or the shower has an L-shape, the waterproofing membrane can be hard to detail correctly. While the membranes beneath most showers are not sloped, it’s worth the effort to slope the underlayment toward the drain before applying the membrane.
Schedule Follow-up Visits
When it comes to serious issues like waterproofing and framing, getting it right the first time is crucial. When it comes to annoyances, however, the easiest course may be to schedule follow-up quality control inspections. When a house is finished, ask the builder to schedule two follow-up quality inspections—one in six months and the other in a year. During the six-month inspection, they should look for anything unusual, like abnormal settling, and address those issues within two weeks. At the 12-month inspection, they should take care of all the cosmetic stuff. A new home needs to go through a heating and cooling cycle in order to reach equilibrium, then they can fix nail pops and such, and they will stay fixed.
A Professional Structural Inspection
BUSTAMANTE ENGINEERS
structural inspections allow the property owner to take advantage of our expertise by allowing us to inspect and evaluate the structural conditions that are of concern. We approach each and every situation in a unique manner bringing forth many decades of engineering experience to assist the homeowner and resolve their issues. Click to contact us online or call 215-340-6990 today and minimize the potential for unpleasant surprises in the future!
SHARE CONTENT
Bustamante Blog
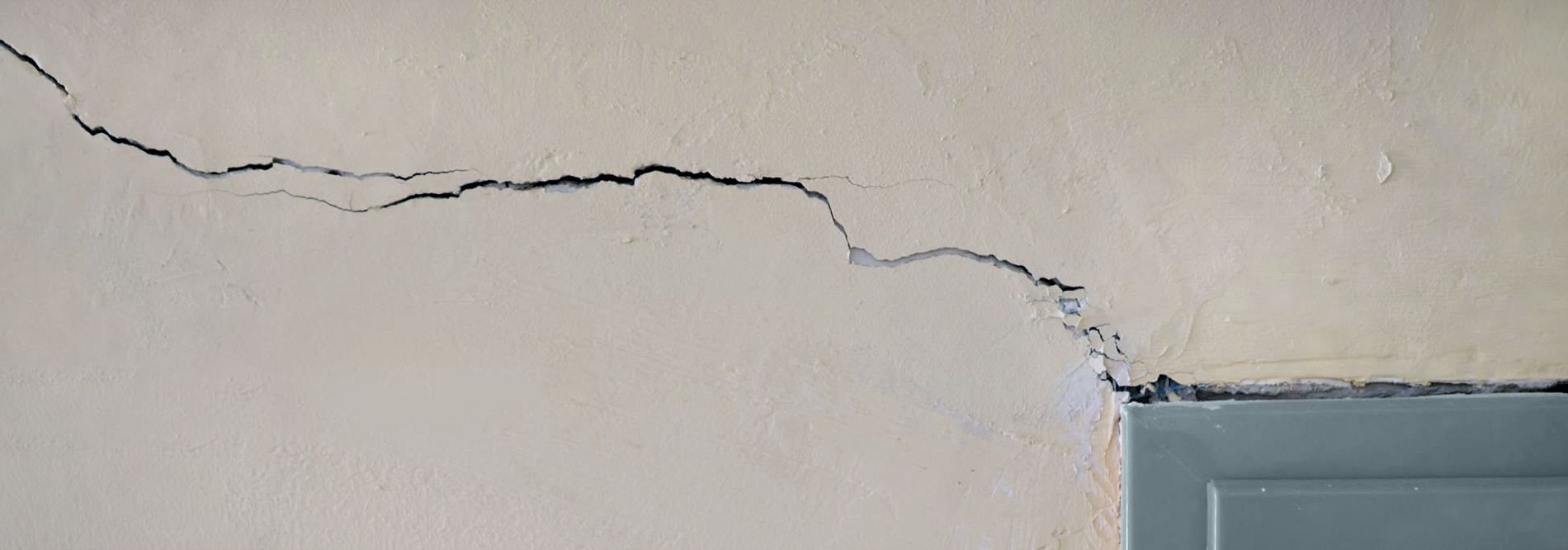
Cracks in walls can be a confusing sight for homeowners, as they may wonder if the cracks are harmless or indicative of structural problems. The key to proper repair and prevention lies in understanding what type of crack it is and its cause. Not all wall cracks should raise equal levels of concern. Whether hairline or larger, vertical or diagonal, each crack tells a unique story about the state of your house’s structure and the external factors affecting it...
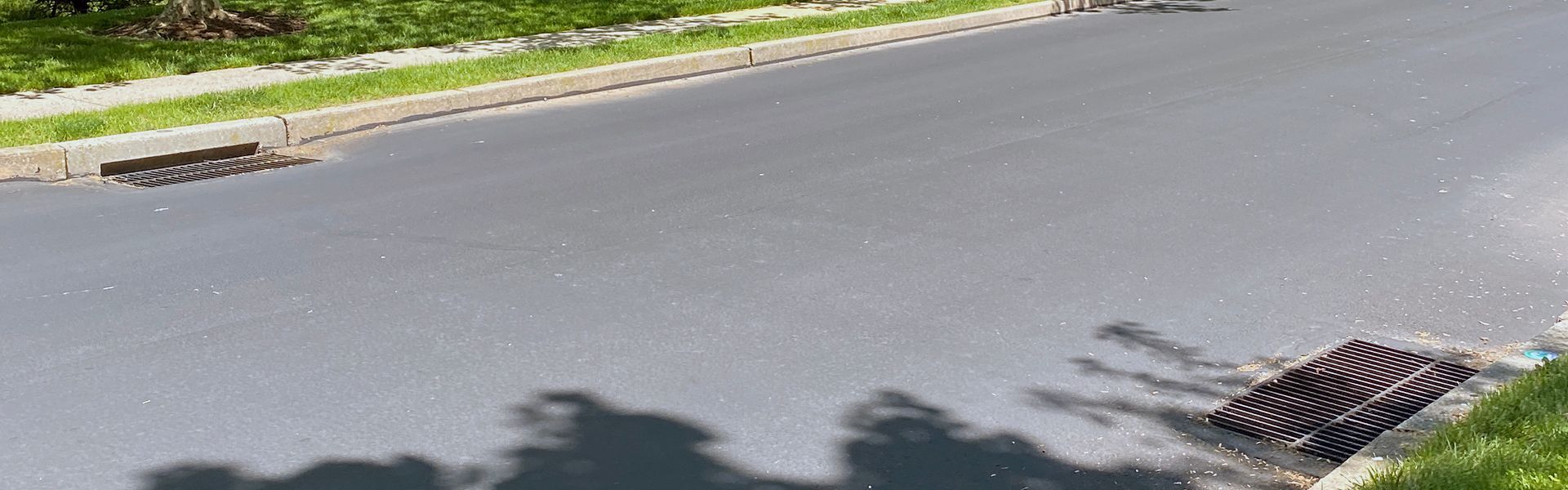
The BUSTAMANTE ENGINEERS Inc. project that we are highlighting this month is CMP pipes that deteriorated and caused a portion of the pipe to collapse, and the necessary funding to complete the project. These four pipes were initially installed to allow for an existing creek to continue flowing underneath a roadway. The project was pertinent as one of the four had already collapsed and the remainder of the pipes were in a similar disrepair. The cost of replacing the 400 linear feet of pipe was a significant undertaking but made possible with the assistance in the form of a loan received from Pennsylvania Infrastructure Investment Authority (PENNVEST).
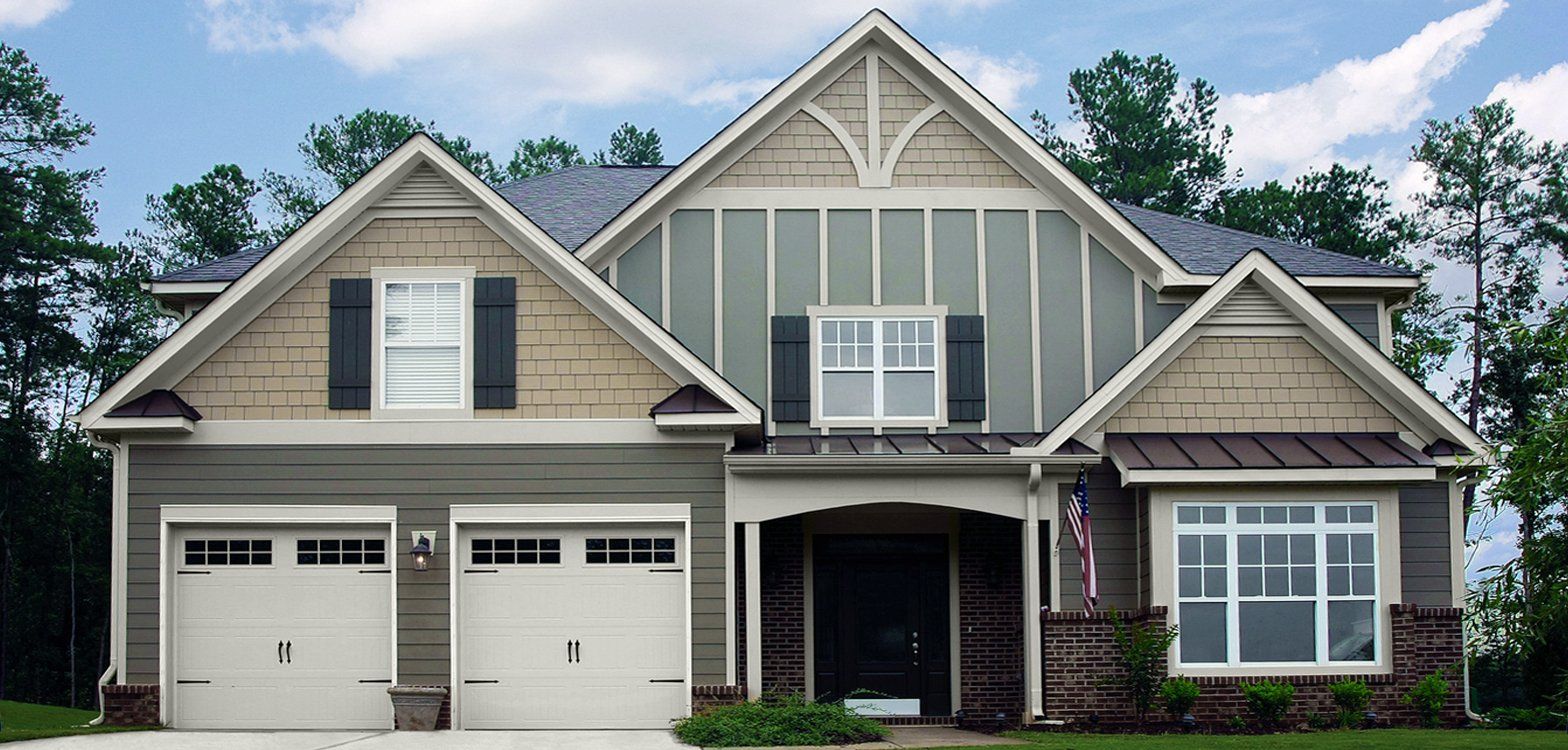
From the initial site analysis to the final inspection, professional engineers ensure that every aspect of a residential renovation is structurally sound, safe, and compliant with all relevant regulations. Engineers also contribute to modern energy efficiency goals by designing systems and structures that reduce environmental impact and enhance energy efficiency. Their role is not only about ensuring the technical aspects of the renovation but also about providing peace of mind to homeowners, knowing that their home is in capable hands.
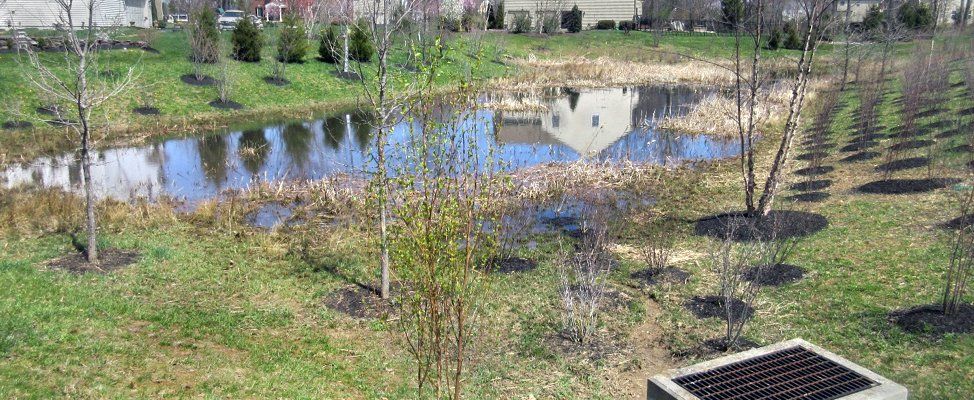
Any impervious surface, including items such as roads, roofs, or sidewalks, does not allow water and snow to drain into the soil and thus increases the amount of stormwater runoff. Common practice is to prevent the stormwater runoff from traveling off the developed site, making detention or retention basins necessary...